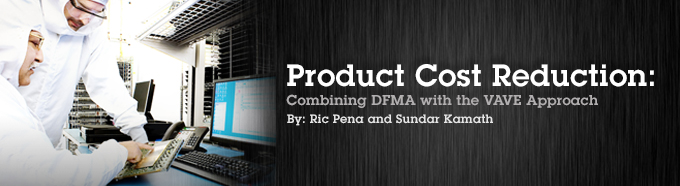
An OEM Designer’s Cost Dilemma
Driven by business and time to market needs, Original Equipment Manufacturers (OEMs) must also meet the performance targets of the product they are designing. Starting from the concept phase, OEMs must ensure the product fulfills customer and market requirements. Often, the designer places very little, if any, emphasis on the product’s component selection, fabrication or ease of assembly. Consequently, the company resolves issues of poor manufacturability only after the product is designed – significantly reducing opportunities for cost savings.
Integrate Manufacturability and Supply Chain Concepts Early
Based on our industry experience, integrating Design for Manufacture and Assembly (DFMA) concepts early into the design cycle, or Early Involvement of DFMA (EI-DFMA) can lead to significantly higher cost savings – between 25% and 40% at the component level. DFM analysis also identifies cost avoidance opportunities.
To meet time to market requirements, initiate EI-DFMA with your manufacturing partner to incorporate cost savings ideas during the first design iteration. While the preliminary design may be rough and incomplete, it is a good basis for concept reviews so you can build management support for full scale development. Once approved, OEM engineers should ensure the product meets functionality and cost targets in its first design cycle, without the option of additional design re-spins. The chances of meeting cost goals early on are much greater if the OEM initiates EI-DFMA with the manufacturing partner. Together, they can define product, material, fabrication, assembly processes and “what-if” scenarios on cost trade-offs versus feature, function, form and appearance. The manufacturer can then provide options for cost reduction and product manufacturability features that optimize design choices.