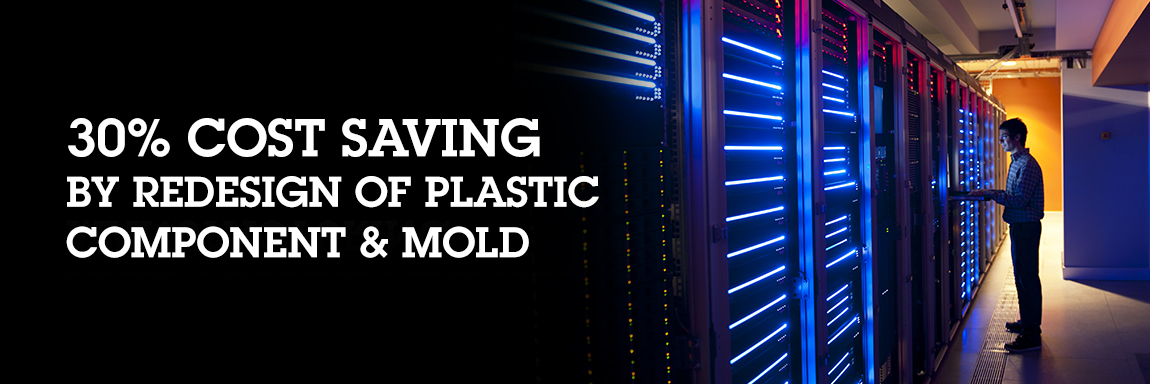
THE CHALLENGE
A tier one data storage OEM needed to reduce cost on every element of a new system. The plastic front bezel is very visible and the cosmetic finish is critical. It is painted a flat black that magnifies any imperfections and the requirement is that the surface is free from sink marks and blemishes.
WHY SANMINA
A scientific molding approach and 40+ years plastic injection molding experience gave the customer tremendous confidence in Sanmina’s ability to deliver quality plastics cost effectively. In addition, Sanmina’s ability to assemble and test the complete server as well as manufacture individual plastic components & metal enclosures greatly simplified the supply chain.
SANMINA’S APPROACH
- The customer engaged Sanmina at an early stage in the product design.
- Sanmina’s injection molding tool design engineers developed a concept to manufacture three plastic components in one mold.
- They developed a 3D model and convinced the customer to alter the design.
- A cross functional engineering team with skills including tooling design, resin expertise, manufacturing process development and quality was established.
- The team used a scientific molding approach to select the resin, design the tooling and develop the manufacturing process.
- Simulation tools were used to analyze flow time, pressure and temperature in the mold during the tool design phase.
- Sequential valve gating was used to eliminate cosmetic blemishes such as sink development.
- A secondary benefit of manufacturing three parts in one mold eliminated the need for alignment and saved time during system build.
RESULTS
- $25k cost saving on tooling.
- 30% cost reduction on plastic manufacture.
- 20% reduction in bezel assembly time during system build.
- The management of components in the supply chain was reduced from two to one.