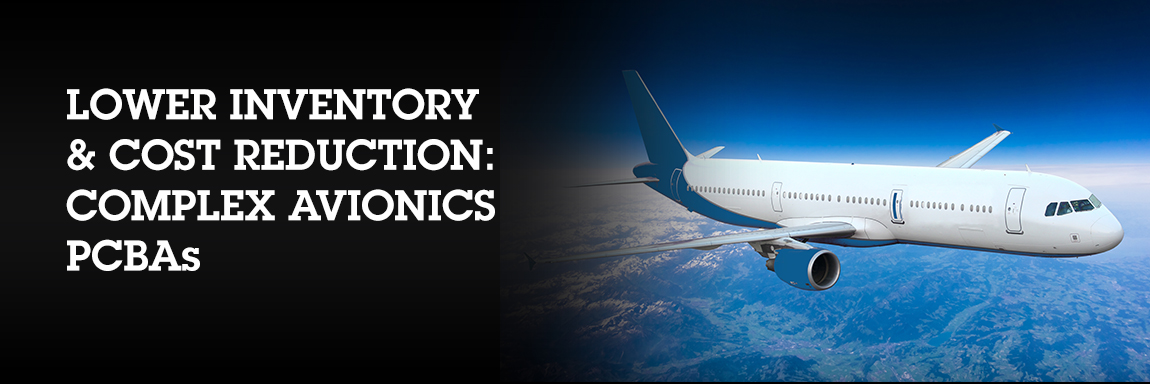
THE CHALLENGE
A tier one avionics company needed to broaden their product and service offerings without additional manufacturing investment by transferring PCBA production to an EMS partner. These PCBAs are the core of avionics systems on board the worlds best known commercial and defense aircraft. There were 200 PCBAs with relatively low volumes, ranging from 5 to 5000 per year. Compliance with AS9100 standards was a requirement. Some of the challenges included:
- High complexity: multiple BGAs on the PCBAs; up to 16 layers on some PCBs; long form factor on others; requirements for conformal and silicone coating.
- The transition of the supply chain involved more than 200 suppliers and over 5,000 components.
- Significant number of obsolete components. Some PCBAs had already been in production for more than 5 years and the product lifetime expectation was an additional 10 years.
WHY SANMINA
Sanmina was recommended by another leading aerospace company; and the customer saw the following benefits with Sanmina:
- Proven experience in the aerospace and defense industry
- Manufacturing processes, supporting tools and IT systems fully compliant with AS9100.
- AS 9100 regulatory compliant product transfer and documentation procedures, refined over two decades.
- Demonstrated experience in dealing with the challenges of low volume high mix manufacturing, advanced technology and numerous obsolete components.
SANMINA’S APPROACH
Sanmina has developed a robust product transfer methodology, refined over many years. Key elements include:
- Formation of a cross-functional team between the customer and Sanmina with representatives from regulatory/quality, engineering, operations, materials and commercial functions.
- A methodology that follows a detailed phase gated plan; based on experience from over 3,200 product transfers completed each year.
- Robust tools to manage all aspects of the program including material availability, manufacturing, test equipment, training, process development, process verification and test, first articles, risk mitigation and contingency management.
Specific requirements for highly reliable manufacturing of complex avionics PCBAs included:
- Transfer of existing equipment to leverage existing validations
- PCBA conformal coating solutions
- Development of a Failure Effect Mode Analysis and resulting risk mitigation
The supply chain was redesigned to optimize cost and reduce risk by:
- Conducting an analysis of the Bill of Materials and Approved Manufacturer List.
- Placing last-time-buy orders for certain components and working with component manufacturers to identify alternative components
RESULTS
- $10M of fixed cost converted to variable cost.
- Customer inventory was reduced by more than $5M.
- The transfer of production created an additional 1,500 square meters of facility space at the customer’s location for advanced systems integration and test.
- Sanmina met all delivery and schedule requirements, and complied with AS9100 regulatory standards.
- Based on the success of these transfers, the customer asked Sanmina to take responsibility for production from another facility.