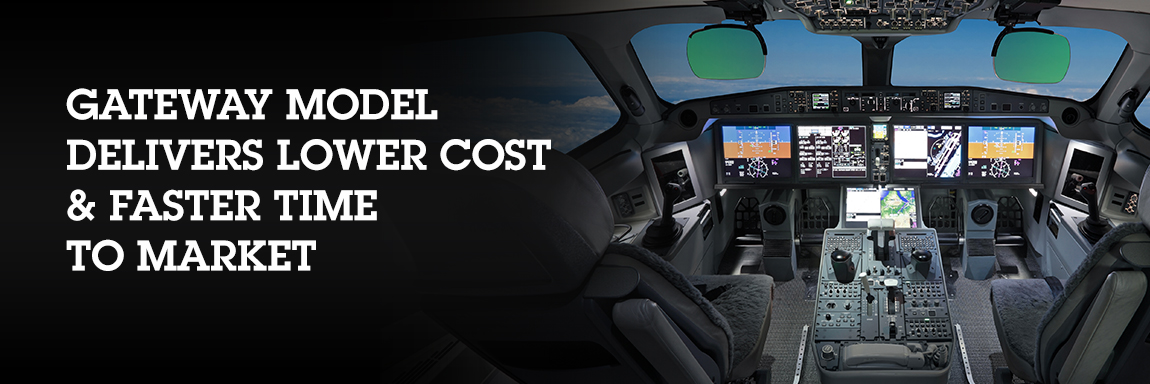
THE CHALLENGE
A major supplier of avionics systems to the world’s best known aircraft manufacturers wanted to outsource production, minimizing investment in capital equipment and overhead to support manufacturing. They also needed fast time to market, local support during product development and the benefits of volume manufacturing in a low cost region. Avionics products face a number of significant challenges throughout their lifecycle.
- The design, supply chain management and manufacturing must comply with the stringent requirements of AS9100.
- Aircraft have an operational life of many decades. Longer product lifecycles require extended engineering support, availability of spares for longer periods and solutions to the challenge of component obsolescence.
- Avionics products are highly complex with as many as 20 layers in the PCB and require expert design and manufacturing services.
- The product portfolio profile is high mix with more than 60 different products, low annual volumes ranging from 1 – 700 units and over 130 suppliers.
WHY SANMINA
The customer had confidence in choosing Sanmina:
- 50 years of experience in design and manufacturing of aerospace products in Sanmina’s SCI division.
- AS9100 Certified in 15 locations world-wide including Europe and low cost regions.
- NADCAP Certified in several manufacturing sites.
- Sanmina’s end-to-end services throughout the product lifecycle ensure that the product can be supported during prototype, NPI, and volume production.
- An established approach to the challenge of obsolete components, for products having a 10-20 year service life
SANMINA’S APPROACH
Sanmina developed a New Product Introduction (NPI) Gateway Services model for the customer that minimized time to market. In the gateway concept a Sanmina manufacturing site in close proximity to the customer design team launches the product and then transfers production to another site in a low cost region when the product is stable. Key elements of the gateway model include:
- An AS9100 and NADCAP certified gateway site close to the customer design team was chosen to support the introduction of new product designs.
- The Gateway site manufactures new product prototypes, conducts design for manufacturing analysis, develops Failure Mode Effect Analysis, designs the manufacturing & test processes and produces the product until stable enough for mass production.
- Advanced engineering support is provided by Sanmina in areas such as PCB technology, PCB design and product test strategy development.
- Sanmina manages the transfer of production to a lower cost region, using a highly robust transfer process, from the Gateway site to the volume manufacturing site in compliance with all the requirements of AS9100 & NADCAP.
- Sanmina product engineers located at the Gateway site manage all engineering change implementations world-wide.
- One IT system world-wide and common processes minimize risk and enable the seamless transfer of production.
- Component engineering services at the Gateway location pro-actively identify components that will go obsolete by using a Part Change Notice system, establishing component lifecycle agreements with suppliers and conducting a quarterly analysis of lead-times.
RESULTS
In this case, Sanmina’s Gateway model resulted in much faster time to market and other benefits:
- Full Aerospace AS9100 and NADCAP Regulatory compliance in prototype, NPI, transfer and volume production.
- Transfer of volume production to Asia to benefit from lower production costs.
- Business Continuity Management is built into the Gateway model by having two sites capable of manufacturing.
- Retained product knowledge in one organization throughout the product life-cycle.
- End–to-end services such as design support and component engineering maximized the benefits of the outsourced variable cost model. It eliminated the customer’s fixed costs.