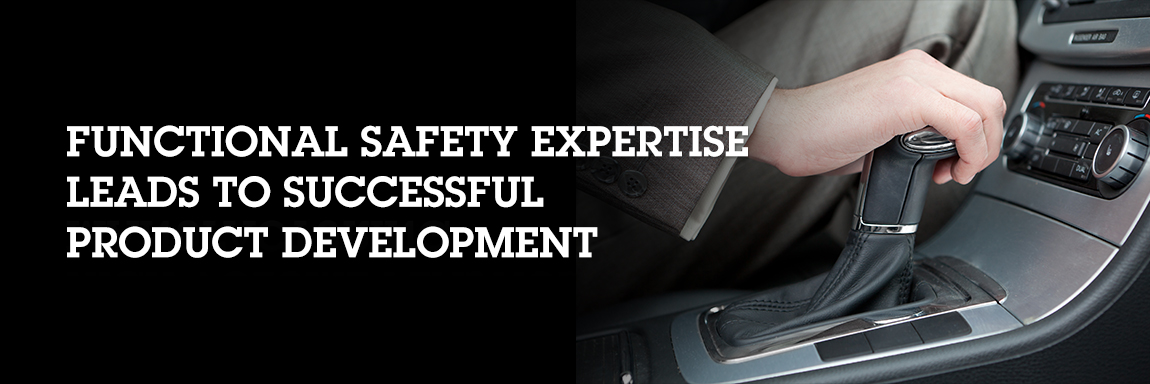
THE CHALLENGE
Automotive manufacturers are subject to increasing regulatory scrutiny to meet the demanding safety standards set by the automotive industry. All automotive designers and manufactures must adhere to an automotive functional safety standard, ISO 26262. For every step of the supply chain, component engineers must assess and control the reliability for automotive parts that may pose a functional safety risk. One leading automotive supplier needed to create an ISO 26262 compliant gear shifting system but faced the challenging task of ensuring their design met the rigorous criteria set by the ISO standard. They realized they needed an EMS partner with practical knowledge of the ISO 26262 standard and automotive regulatory requirements to help the company implement a compliant system that met their development schedule. They turned to Sanmina.
SANMINA’S APPROACH
With over 20 years of experience working with automotive regulatory standards, Sanmina has gained practical expertise in developing manufacturing and design processes to deliver compliant products. Our automotive engineers applied extensive experience in functional safety assessment to ensure the company met both compliance and product schedule goals. Sanmina integrated the ISO compliance standard into the company’s automotive development process by:
-
1. Understanding product functional requirements and Automotive Safety Integrity Level (ASIL) related product characteristics defined by the OEM and / or Tier1 company.
2. Conducting a risk analysis on the product design and components, while including the lifetime mission profile of the product and the components used in the design. The approach includes Failure Tree Analysis of the product, components and even the silicon.
3. Contacting component manufacturers to understand and discuss functional safety support and compliancy of their components at the product’s defined ASIL level.
4. Identifying any components which do not directly support the required ASIL level. This allows the product designer to focus on the Safety Element out of Context (SEooC) and to develop methods to ensure all failure modes are fully controllable in compliance with the ISO 26262 requirements.
5. Performing a Lifetime Consumption Analysis on all relevant gear shifting elements throughout the entire design and manufacturing process to validate the expected product lifetime and to ensure functional safety standards are met.
6. Implementing all ISO 26262 compliance requirements for design, manufacturing and test with all other automotive regulatory requirements, including the IATF 16949, APQP and PPAP.
SOLUTION: A PRACTICAL GUIDE FOR COMPLIANCE BEST PRACTICES
Sanmina developed a step-by-step guide, which included the necessary templates and tools, to enable the company to successfully implement a process which met functional safety requirements. Our long-standing partnership with leading Automobile OEMs, Tier-1 automotive companies and strong expertise across a range of safety critical industries, places Sanmina at the forefront of industry-specific regulatory requirements.
RESULTS
By adopting Sanmina’s functional safety implementation guidelines, the company developed an effective, ISO 26262 compliant gear shift system on schedule. As a leader in regulatory best practices, Sanmina also trained the company’s staff on functional safety compliance. Due to its success, the company integrated Sanmina’s implementation process into all future product development programs.