AFTERMARKET & REMANUFACTURING SERVICES FOR OEMs
For high tech OEMs that need electronic repair services for mission critical systems, Sanmina provides a global network of world class repair facilities. We create customized repair solutions to manage customers’ in-warranty and out-of-warranty requirements. The solutions can include spares management, RMA management, advanced exchange and specific turnaround times to support our customers service level agreements with their end customers while at the same time minimizing inventory.
REPAIR & REMANUFACTURING PRODUCT EXPERTISE
Sanmina has decades of experience in aftermarket repair and refurbishment of a wide range of products including those shown in the examples below.
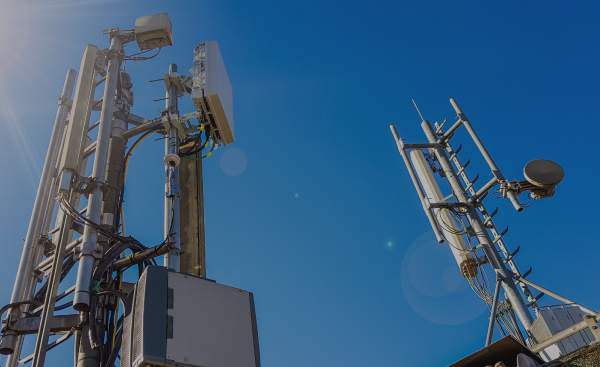
Sanmina has been providing Communications Support Services for decades. We support legacy products from wireline and 2G to leading edge 5G base stations, mMIMOs and cloud based products.
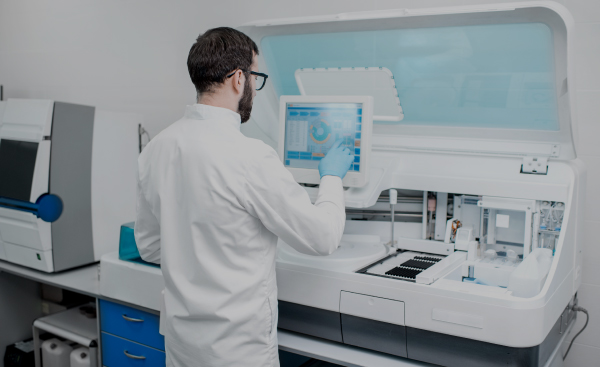
With a global network of ISO 13485 and FDA registered facilities, Sanmina is highly experienced in servicing a wide range of medical systems including couches as well as clinical chemistry, blood management, imaging and lab diagnostics systems.
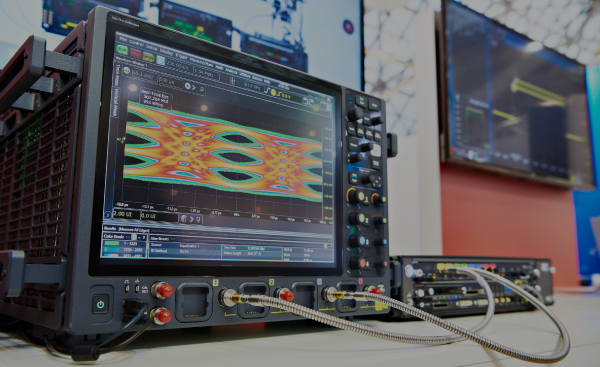
Sanmina possesses extensive experience in electromechanical systems including 3D printers, kiosks, gaming systems, test equipment, security and safety products.
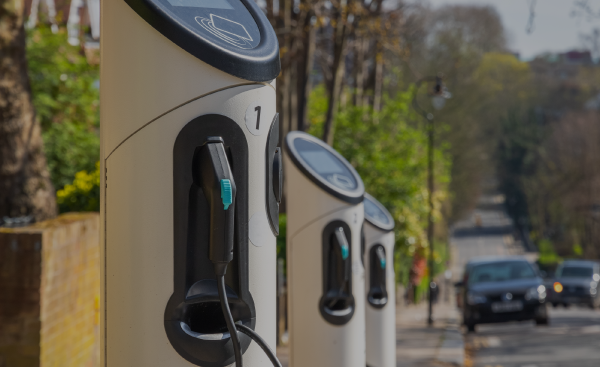
Sanmina is one of the largest providers of energy solutions for OEMs including power distribution and management systems, smart meters and electrical car chargers.
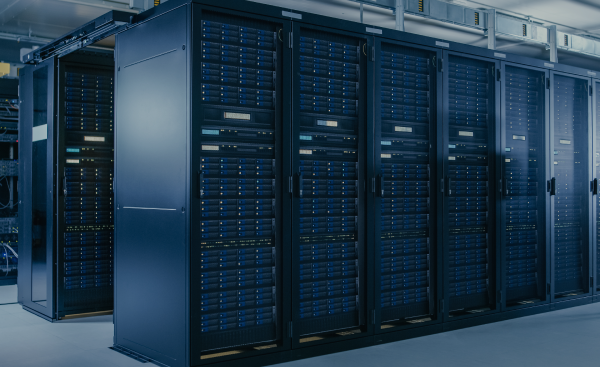
Sanmina builds and maintains large scale high-powered & secure computers and systems for cloud infrastructure, social media and security applications.

Sanmina’s supply chain systems and logistics infrastructure efficiently drive fast turnaround times to meet the demands of the high volume environments of mobile and handheld computer businesses.
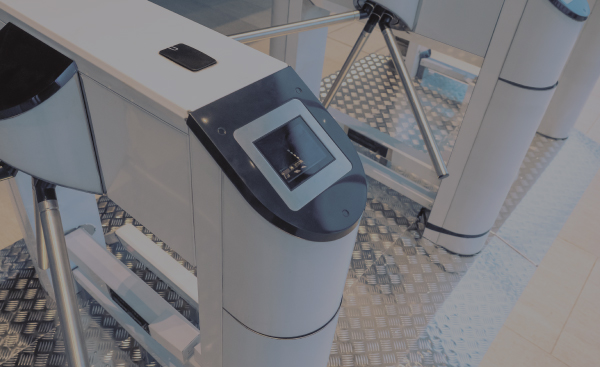
Sanmina’s extensive technology experience allows expert repair and refurbishment solutions that incorporate knowledge of both mechanical and electronic repairs.
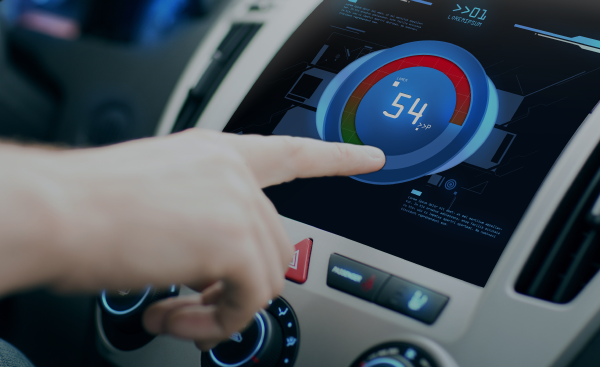
Sanmina’s robust Quality System supports major OEMs, tier 1 and tier 2 suppliers with solutions to improve product reliability and cost in the highly demanding automotive market.
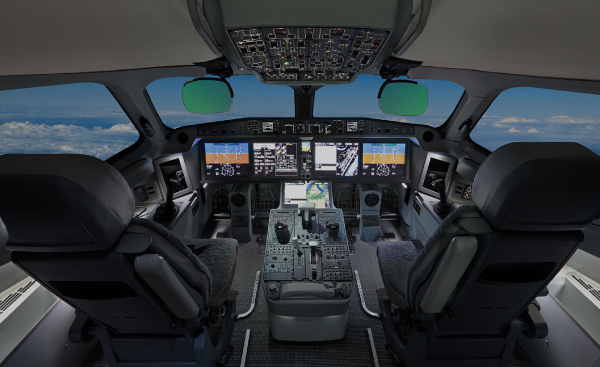
Long-standing support of mission-critical high-reliability products for military, commercial aviation, defense applications, space-flight and security programs.